Dowty Propellers’ Field Service Engineers find new ways to deliver customer support during the COVID-19 pandemic
March 25, 2021
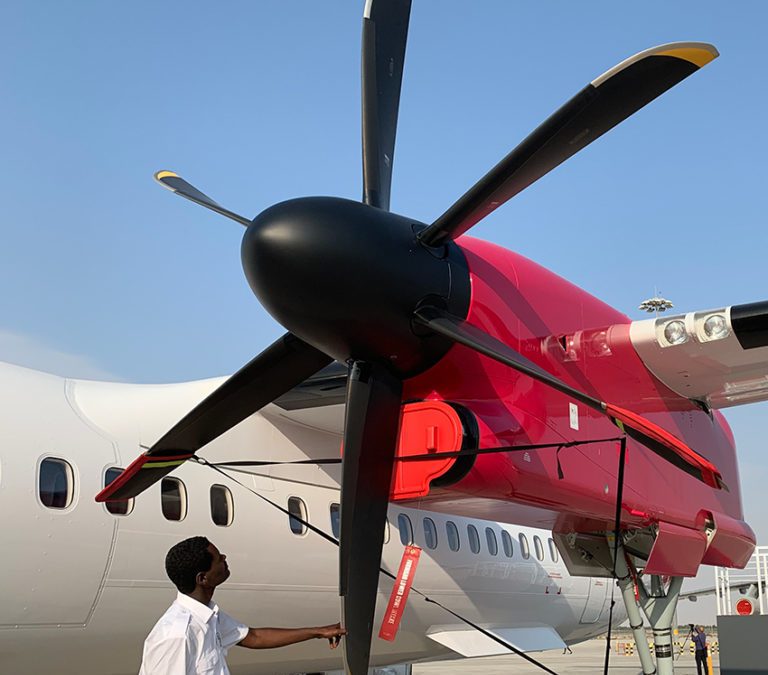
The COVID-19 pandemic has posed unique challenges to the Dowty Propellers team of 70 global Field Service Engineers as they have navigated numerous roadblocks to continue to deliver high-levels of support to customers.
The team has had to come up with new engineering solutions – particularly if a customer is based in a region to which travel is not allowed. Says Kerry Garfield, Global Field Services Leader: “With operating economics for an aircraft even more challenging than usual in a COVID world, our engineers have worked with customers to develop solutions so aircraft can safely remain in service without consuming excessive spare parts. The few airlines that are permitted to fly can’t afford to have aircraft out of service, and our field service teams have engaged in preventative maintenance using digital technology to help our customers achieve that goal.”
He adds: “Where travel to a customer was unavoidable, we worked with local governments to find a way. Our dedicated engineers had on occasion to break travel into stages and really went the extra mile by isolating for up to three weeks before reaching a customer.”
A further challenge for the team was a potential showstopper. To perform repairs in the field, all engineers must achieve external certification from a non-destructive testing (NDT) body annually. This involves a practical exam which Dowty Propellers engineers from across the world travel to attend. They are observed in person by the NDT body before it awards or renews accreditation. Without the appropriate certification, the team of engineers could not travel out to the field and help our customers.
The usual accreditation sessions were not allowed to take place during the pandemic, posing a huge dilemma. Not wanting to let this stop us from helping our customers, we worked with the NDT accreditation board to develop virtual workshops and exams via video-link to ensure our engineers could complete the necessary exams, achieve accreditation and continue to operate in the field and keep our customers in operation.
Aaron Hopkins is the Customer Program Engineer for Japan and European regions. “COVID has really made my job challenging as I would normally travel out to my operators to deliver help with training or perform on-wing repairs,” he explained. “I have increased my use of technology to maintain strong customer relationships. By using virtual meetings and conducting virtual working sessions, I can work through technical issues as though my customer and I were side by side. Regular calls with operators keep me in touch and we have performed more repairs at our Gloucester headquarters than we might normally. I am looking forward to getting back out on the road and seeing my customers in person.”